Páginas
domingo, 21 de septiembre de 2014
viernes, 19 de septiembre de 2014
Identificación, Prevención y Tratamiento de las Fisuras
Identificación de las Fisuras
Fisura en la parte superior de las vigas:
Siguiendo la línea de los estribos. Se debe al calentamiento de los hierros por el sol, que hace perder la humedad a la mezcla en la zona de contacto con los mismos.
Fisuras de retracción hidráulica por contracción de fraguado:

Fisuras de retracción hidráulica por secado lento:
Aparecen en piezas estructurales cuyos movimientos de retracción están impedidos por su empotramiento o -en el caso de los pavimentos-, por su adherencia al terreno. En éstos, si no se les hacen las juntas de contracción con las separaciones adecuadas, aparecen espontáneamente, a intervalos regulares, en dirección normal al sentido de marcha y de un espesor regular.
Fisuras de entumecimiento:
Son provocadas por un aumento del volumen del hormigón que puede deberse a materiales expansivos incluidos en la masa. Las más conocidas son las expansiones producidas por la reacción álcali agregado (Alcali-sílice) que destruyen velozmente la estructura; otras más lentas como el ataque por sulfatos, la oxidación de los hierros de refuerzo o elementos férricos empotrados en la masa del hormigón, y el efecto de congelación y deshielo.
Prevención de las Fisuras
En Sub bases y Encofrados
Se deben eliminar de la superficie, todos los restos de material suelto y partículas blandas. La sub base de las losas debe de ser un suelo bien compactado o a base de un relleno granular compactado con rodillo, vibrado o apisonada. La losa y la base deben tener cierta pendiente para facilitar un buen drenaje. Las sub bases llanas y lisas evitan la formación de fisuras. El encofrado debe de ser construido de manera que pueda resistir la presión del hormigón sin deformarse. Las láminas de curado de polietileno aumentan el sangrado y por tanto el fisurado de hormigones con exceso de agua. Cubrir las láminas de curado con una capa de arena humedecida de 2,5 a 5 cm. de espesor para reducir el sangrado. Humedecer la sub base, el encofrado y las armaduras inmediatamente antes de colocar el hormigón.
En Hormigón
Utilizar hormigón de plasticidad moderada (no más de 12 cm.). Evitar siempre el añadido posterior de agua con amasado suplementario. Si el hormigón debe ser fluido con más de 17 cm. de cono, las proporciones de la mezcla deben modificarse, utilizándose mezclas especiales con superplastificantes que eviten un sangrado excesivo, segregaciones y bajas resistencias. Especificar siempre hormigón aireado para losas al exterior que puedan sufrir heladas.
Evitar el uso de cemento de fraguado o endurecimiento rápido en situaciones climáticas desfavorables.
En Acabado
No realizar operaciones de acabado si hay agua en la superficie. El nivelado inicial debe de ser seguido de un rápido fratasado. Para un mejor agarre en superficies exteriores, efectuar un acabado con escoba. Si la evaporación es excesiva, reducirla en lo posible para evitar la fisuración por retracción plástica. Cubrir el hormigón con una tela húmeda o con hojas de polietileno durante las operaciones de acabado si las condiciones atmosféricas son severas.
En Curado
Inicie el curado tan pronto como sea posible, manteniendo húmeda la superficie de los elementos de hormigón. Rociar la superficie con un líquido de curado o cubrirla con telas húmedas al menos durante tres días.
En Juntas
Para controlar los efectos de contracción y expansión debido a los cambios de temperatura y/o humedad, deben de construirse, mediante sierra, disco o con herramientas adecuadas, unas juntas de construcción del grueso de la losa, con una separación entre ellas no superior a 30 veces el grueso de la misma. Con frecuencia deben de ponerse las juntas próximas unas a las otras para evitar largas áreas estrechas. La longitud de estas no debe de ser mayor de 1,5 veces el ancho. Las juntas perimetrales deben de incluirse en aquellos sitios donde puedan existir restricciones para los movimientos verticales u horizontales, tales como la unión de muros y suelos, columnas o pavimentos. En este caso deben ser profundas y se construyen insertando algún tipo de elemento barrera para prevenir la adhesión entre la losa y los otros elementos.
Recubrimiento de las Armaduras
Las fisuras en el Hormigón Armado debidas a la corrosión de las armaduras por formación y expansión de oxido de hierro, deben evitarse proporcionando el recubrimiento mínimo fijado por normativa.
Riego
Abundante riego previo de la base en pavimentos, y de los encofrados en losas de edificios.
Agregados
Empleo de agregados previamente humedecidos. Evitar un exceso de finos en los agregados del hormigón.
Aditivos
Usar aditivos químicos fluidificantes o retardadores de fraguado que permitan disminuir la necesidad de agua de mezclado y la caída del asentamiento en el Cono de Abrams antes de descargar.
Agua
Evitar exceso de agua de mezclado. No echar agua sobre el hormigón para facilitar la tarea de terminación.
Tratamiento de las Fisuras
El tiempo caluroso con varios días por encima de los 30º C, los vientos secos sostenidos y la baja presión atmosférica, hacen que la fisuración se desarrolle aun antes de haberse secado totalmente el agua de exudación de la superficie del hormigón.
Es un caso extremo en que la experiencia indica que hay que dejar que la fisuración se produzca, y completar con la terminación normal. Luego que terminó el proceso de fraguado (alrededor de 5 horas después de la terminación y hasta 24 horas después) pueden repararse las fisuras preparando una lechada rica en cemento Portland, con una consistencia que le permita penetrar en las fisuras llenándolas íntegramente; se las rellenará manualmente ayudándose con un cepillo o escoba.
Luego que seque este material, se procederá al curado normal de la estructura tal como se tenía previsto. Con este tratamiento, la fisura desaparecerá definitivamente
martes, 16 de septiembre de 2014
¿Sabes por qué triunfó el hormigón armado?
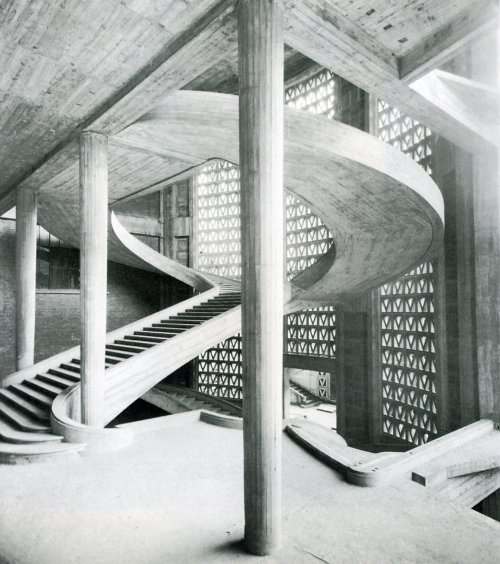
Para explicar el porqué del uso generalizado del hormigón armado en la arquitectura del último siglo, quizá habría que imaginar como sería la construcción si no existiese el hormigón, esa mezcla de arena, piedra, cemento y agua que está presente en prácticamente todos nuestras casas.
A falta de conglomerantes como yesos, cales o cementos, que unan los materiales entre sí, deberíamos utilizar necesariamente elementos masivos para el soporte de nuestros edificios, muros y grandes masas de piedra o elementos que por gravedad -o por su propio peso, que diría un castizo- conformasen el apoyo de forjados o vigas sobre ellos.
Estos últimos no podrían tener más longitud sin incurrir en espesores excesivos y poco manejables que la de un elemento que pudierse soportar sobre él al pasearse por su punto un medio, el equivalente a tres o cuatro personas adultas sin deformarse más allá de 1/500 -aproximadamente- de la luz o longitud de esa viga, es decir en una viga de 5 metros (5000 milímetros) no podría deformarse más de 10 milímetros.
Mediante la utilización del hormigón, armado interiormente con elementos de acero que soportan mejor estas flexiones y tracciones en la parte inferior de las vigas, conseguimos por una parte el manejo en la obra de elementos más pequeños que no grandes vigas de madera o acero y por la otra, gracias a la virtud del hormigón de fraguar con la forma del molde que empleemos, lograr elementos arquitectónicos que no están limitados a las lineas rectas o a los arcos de descarga, ofreciendo una mayor libertad en el el diseño de espacios y edificios, además de lograr mayores luces y resistencias con menores espesores.
Pues bien, aunque podemos encontrar distintos materiales conglomerantes desde las antiguas civilizaciones egipcias, griegas o romanas, no es hasta que se implanta el uso generalizado del hormigón, ya en el siglo XIX, merced a avances industriales tales como la mejora de los hornos que permitían la fabricación del cemento y la inclusión del acero en la masa del hormigón para aumentar la resistencia a flexión – y así poder utilizarlo en elementos más largos que resistan la flexión- cuando podemos considerarlo un sistema cotidiano de construir arquitectura.
Si hay dos personajes que considero claves en la implantación del uso de hormigón en edificación son Auguste Perret (1874-1954) y Le Corbusier (1877-1965) , el primero por apostar decididamente por el uso del hormigón desde la empresa constructora que creó con su hermano y el segundo por establecer -gracias a que el hormigón se lo permitió- la planta libre de muros mediante el uso de pilares (1). Algo que de la que ya no somos capaces de prescindir.
domingo, 14 de septiembre de 2014
Estructuras del hormigon armado
Como señalamos anteriormente el concreto armado es la combinación del concreto y el acero en armadura para que juntos formen un material combinado e indivisible. La colocación de las armaduras depende de la ubicación de la zona de tracción, es decir del lugar donde las vigas, columnas, voladizos o demás componentes se flexionarán; asimismo en los cimientos tipo losa corrida, las varillas de acero longitudinal y transversal se ponen en la parte inferior de la losa con el fin de resistir los esfuerzos de tracción y evitar las rajaduras.
Uso del hormigon
Las construcciones utilizan un gran número de materiales que sirven para diferentes cosas, combinados, los materiales dan como resultado una construcción fuerte y duradera, lo que hay que saber es cómo mezclarlos perfectamente para lograr el resultado deseado.
Uno de estos importantes materiales para construcción es el hormigón. El hormigón es también conocido como concreto, es un material compuesto, se utiliza en las construcciones especialmente como aglomerante; es común que a este se le agreguen partículas de algún agregado, agua y algunos aditivos específicos que le ayudan a ser más resistente. Generalmente el aglomerado que se le agrega al hormigón es cemento portland con agua para que se hidrate la mezcla y sea más manejable.
Ahora bien, el hormigón armado es una técnica que se utiliza para diferentes tipos de construcción, este consiste en la utilización de hormigón reforzado por medio de mallas de acero o bien barras de acero que se conocen como armaduras. Hay quienes utilizan otros materiales como fibras plásticas o de vidrio, hay quienes optan, para la mejor resistencia de la construcción, fibras de acero. El acompañamiento del hormigón depende de el esfuerzo y trabajo al que estará sometida la construcción.
Es un material de uso común, lo encontramos en edificios, túneles, obras industriales, puentes, presas, casas, etc., esto debido a que es un material que cuenta con muy buenas propiedades como ser bastante moldeable y resistente a esfuerzos de compresión; es también un material que dura en muy buen estado con el paso del tiempo. Aquellas construcciones acompañadas con acero, le ayudan a la pieza a tener mayor ductilidad, esto puede ser útil en los casos de desgaste de una parte de la construcción, ya que presentarán una deformación notoria antes de que presenten la falla como tal.
Pero el uso del hormigón no es algo nuevo en el mundo de las construcciones, su utilidad ha sido reconocida desde 1854, cuando el constructor William Wilkinson empezó a utilizarlo para darle mayor resistencia y durabilidad a las construcciones de todo tipo, sin embargo, fue hasta 1861, que un constructor francés decidió aplicar el uso del hormigón a techos, paredes, bóvedas y tubos, con lo que las construcciones se veían y se sentían mucho más seguras, por lo que rápidamente empezó a ganar popularidad entre los constructores de todas partes del mundo.
Es importante saber cómo combinar bien el hormigón dependiendo de la construcción que requiramos edificar ya que un error en el cálculo puede costar miles de vidas.
Uno de estos importantes materiales para construcción es el hormigón. El hormigón es también conocido como concreto, es un material compuesto, se utiliza en las construcciones especialmente como aglomerante; es común que a este se le agreguen partículas de algún agregado, agua y algunos aditivos específicos que le ayudan a ser más resistente. Generalmente el aglomerado que se le agrega al hormigón es cemento portland con agua para que se hidrate la mezcla y sea más manejable.
Ahora bien, el hormigón armado es una técnica que se utiliza para diferentes tipos de construcción, este consiste en la utilización de hormigón reforzado por medio de mallas de acero o bien barras de acero que se conocen como armaduras. Hay quienes utilizan otros materiales como fibras plásticas o de vidrio, hay quienes optan, para la mejor resistencia de la construcción, fibras de acero. El acompañamiento del hormigón depende de el esfuerzo y trabajo al que estará sometida la construcción.
Es un material de uso común, lo encontramos en edificios, túneles, obras industriales, puentes, presas, casas, etc., esto debido a que es un material que cuenta con muy buenas propiedades como ser bastante moldeable y resistente a esfuerzos de compresión; es también un material que dura en muy buen estado con el paso del tiempo. Aquellas construcciones acompañadas con acero, le ayudan a la pieza a tener mayor ductilidad, esto puede ser útil en los casos de desgaste de una parte de la construcción, ya que presentarán una deformación notoria antes de que presenten la falla como tal.
Pero el uso del hormigón no es algo nuevo en el mundo de las construcciones, su utilidad ha sido reconocida desde 1854, cuando el constructor William Wilkinson empezó a utilizarlo para darle mayor resistencia y durabilidad a las construcciones de todo tipo, sin embargo, fue hasta 1861, que un constructor francés decidió aplicar el uso del hormigón a techos, paredes, bóvedas y tubos, con lo que las construcciones se veían y se sentían mucho más seguras, por lo que rápidamente empezó a ganar popularidad entre los constructores de todas partes del mundo.
Es importante saber cómo combinar bien el hormigón dependiendo de la construcción que requiramos edificar ya que un error en el cálculo puede costar miles de vidas.
lunes, 8 de septiembre de 2014
domingo, 7 de septiembre de 2014
Historia del Hormigom
Historia
del Hormigón
La
invención del hormigón armado se suele atribuir al constructor William
Wilkinson, quien solicitó en 1854 la patente de un sistema que incluía
armaduras de hierro para «la mejora de la construcción de viviendas, almacenes
y otros edificios resistentes al fuego». En el 1855 Joseph-Louis Lambot publicó
el libro «Les bétons agglomerés appliqués á l'art de construire» (Aplicaciones
del hormigón al arte de construir), en donde patentó su sistema de
construcción, expuesto en la exposición mundial en París, el año 1854, el cual
consistía en una lancha de remos fabricada de hormigón armado con alambres.
François Coignet en 1861 ideó la aplicación en estructuras como techos,
paredes, bóvedas y tubos.
A
su vez el francés Joseph Monier patentó varios métodos en la década de 1860.
Muchas de estas patentes fueron obtenidas por G.A. Wayss en 1866 de las
empresas Freytag und Heidschuch y Martenstein, fundando una empresa de hormigón
armado, en donde se realizaban pruebas para ver el comportamiento resistente
del hormigón, asistiendo el arquitecto prusiano Matthias Koenen en estas
pruebas, efectuando cálculos que fueron publicados en un folleto llamado «El
sistema Monier, armazones de hierro cubiertos en cemento». Que fue
complementado en 1894 por Edmond Coignet y De Tédesco, método publicado en
Francia agregando el comportamiento de elasticidad del hormigón como factor en
los ensayos, estos cálculos fueron confirmados por otros ensayos realizados por
Eberhard G. Neumann en 1890. Bauschinger y Bach comprobaron las propiedades del
elemento frente al fuego y su resistencia logrando ocasionar un gran auge, por
la seguridad del producto en Alemania. Fue François Hennebique quien ideó un
sistema convincente de hormigón armado, patentado en 1892, que utilizó en la
construcción de una fábrica de hilados en Tourcoing, Lille, en 1895.
En
España, el hormigón armado penetra en Cataluña de la mano del ingeniero
Francesc Macià con la patente del francés Joseph Monier. Pero la expansión de
la nueva técnica se producirá por el empuje comercial de François Hennebique
por medio de su concesionario en San Sebastián Miguel Salaverría y del
ingeniero José Eugenio Ribera, entonces destinado en Asturias, que en 1898
construirá los forjados de la cárcel de Oviedo, el tablero del puente de Ciaño
y el depósito de aguas de Llanes.
El
primer edificio de entidad construido con hormigón armado es la fábrica de
harinas La Ceres en Bilbao, de 1899-1900 (aún hoy en pie y rehabilitada como
viviendas) y el primer puente importante, con arcos de 35 metros de luz, el
levantado sobre el Nervión-Ibaizabal en La Peña, para el paso del tranvía de
Arratia entre Bilbao y Arrigorriaga (desaparecido en las riadas del año 1983).
Ninguna de las dos obras fue dirigida por Ribera, quien pronto se independizó
de la tutela del empresario francés, sino por los jóvenes ingenieros Ramón
Grotta y Gabriel Rebollo de la oficina madrileña de François Hennebique.
Diseño
de estructuras de hormigón armado
Hennebique
y sus contemporáneos, basaban el diseño de sus patentes en resultados
experimentales, mediante pruebas de carga; los primeros aportes teóricos los
realizan prestigiosos investigadores alemanes, tales como Wilhem Ritter, quien
desarrolla en 1899 la teoría del «Reticulado de Ritter-Mörsch». Los estudios
teóricos fundamentales se gestarán en el siglo XX.
Existen
varias características responsables del éxito del hormigón armado:
² El
coeficiente de dilatación del hormigón es similar al del acero, siendo
despreciables las tensiones internas por cambios de temperatura.
²
Cuando el hormigón fragua se contrae y
presiona fuertemente las barras de acero, creando además fuerte adherencia
química. Las barras, o fibras, suelen tener resaltes en su superficie, llamadas
corrugas o trefilado, que favorecen la adherencia física con el hormigón.
² Por
último, el pH alcalino del cemento produce la pasivación del acero, fenómeno que
ayuda a protegerlo de la corrosión.
El hormigón que rodea
a las barras de acero genera un fenómeno de confinamiento que impide su pandeo,
optimizando su empleo estructural
CURADO DEL HORMIGÓN
EL CURADO
es uno de los pasos más importantes en la construcción del hormigón, porque un curado correcto aumenta la resistencia del hormigón y la durabilidad.

El curado tiene por objetivo impedir el secado prematuro del concreto, cuyas consecuencias son dobles:
- la reacción química del agua y del cemento se interrumpe por falta del agua necesaria, de modo que el concreto no adquiere las propiedades que su composición permitiría;
- se produce una contracción precoz, generando la formación de fisuras . Al evaporarse, el agua desarrolla fuerzas que generan, en el cemento en fase de endurecimiento, una contracción cuyo valor puede sobrepasar la resistencia a la tensión del concreto en proceso de endurecimiento.
El hormigón se endurece como resultado de la hidratación: la reacción química entre el cemento y el agua. Sin embargo, la hidratación se produce sólo si el agua está disponible y si la temperatura del hormigón se mantiene dentro de un rango adecuado. Durante el período inicial de curación de cinco a siete días después del vertido del hormigón convencional sobre la superficie la humedad debe ser mantenida para permitir el proceso de hidratación. El hormigón nuevo puede ser mojado con mangueras para su remojo, aspersores o cubierto con trapos húmedos, o puede ser recubierto con productos comercialmente disponibles diseñados para el curado, y que sellan la humedad.
Una forma de curar es prolongar la humedad al aplicar tela de arpillera húmeda a la superficie de hormigón conservando la continuamente húmedo por un período de 28 días. Diferentes investigaciones muestran que el hormigón continuamente húmedo, con un curado por un período de 28 días dio lugar a una resistencia a la compresión superior a 4.500 psi. Sin embargo, el mismo hormigón curado permitiendo que el aire de rose constantemente en el mismo período solo se lograron 2.550 psi. Además, la resistencia a la compresión a los 180 días eran en realidad más bajos para el hormigón curado al aire, 2.500 psi, y el hormigón con constante humedad durante el proceso de curado alcanzo una resistencia a la compresión máxima de más de 5.750 psi.
Mejorar el proceso de curado en húmedo

Fraguado y endurecimiento
La pasta del hormigón se forma mezclando cemento artificial y agua debiendo embeber totalmente a los áridos. La principal cualidad de esta pasta es que fragua y endurece progresivamente, tanto al aire como bajo el agua.
El proceso de fraguado y endurecimiento es el resultado de reacciones químicas de hidratación entre los componentes del cemento. La fase inicial de hidratación se llama fraguado y se caracteriza por el paso de la pasta del estado fluido al estado sólido. Esto se observa de forma sencilla por simple presión con un dedo sobre la superficie del hormigón. Posteriormente continúan las reacciones de hidratación alcanzando a todos los constituyentes del cemento que provocan el endurecimiento de la masa y que se caracteriza por un progresivo desarrollo de resistencias mecánicas.
El fraguado y endurecimiento no son más que dos estados separados convencionalmente; en realidad solo hay un único proceso de hidratación continuo.
En el cemento portland, el más frecuente empleado en los hormigones, el primer componente en reaccionar es el aluminato tricálcico con una duración rápida y corta (hasta 7-28 días). Después el silicato tricálcico, con una aportación inicial importante y continua durante bastante tiempo. A continuación el silicato bicálcico con una aportación inicial débil y muy importante a partir de los 28 días.
El fenómeno físico de endurecimiento no tiene fases definidas. El cemento está en polvo y sus partículas o granos se hidratan progresivamente, inicialmente por contacto del agua con la superficie de los granos, formándose algunos compuestos cristalinos y una gran parte de compuestos microcristalinos asimilables a coloides que forman una película en la superficie del grano. A partir de entonces el endurecimiento continua dominado por estas estructuras coloidales que envuelven los granos del cemento y a través de las cuales progresa la hidratación hasta el núcleo del grano.
El hecho de que pueda regularse la velocidad con que el cemento amasado pierde su fluidez y se endurece, lo hace un producto muy útil en construcción. Una reacción rápida de hidratación y endurecimiento dificultaría su transporte y una cómoda puesta en obra rellenando todos los huecos en los encofrados. Una reacción lenta aplazaría de forma importante el desarrollo de resistencias mecánicas. En las fábricas de cemento se consigue controlando la cantidad de yeso que se añade al clinker de cemento. En la planta de hormigón, donde se mezcla la pasta de cemento y agua con los áridos, también se pueden añadir productos que regulan el tiempo de fraguado.
En condiciones normales un hormigón portland normal comienza a fraguar entre 30 y 45 minutos después de que ha quedado en reposo en los moldes y termina el fraguado trascurridas sobre 10 ó 12 horas. Después comienza el endurecimiento que lleva un ritmo rápido en los primeros días hasta llegar al primer mes, para después aumentar más lentamente hasta llegar al año donde prácticamente se estabiliza.
Características Fisicas
- Características físicas del hormigón
Las principales características físicas del hormigón, en valores aproximados, son:
- Densidad: en torno a 2350 kg/m³
- Resistencia a compresión: de 150 a 500 kg/cm² (15 a 50 MPa) para el hormigón ordinario. Existen hormigones especiales de alta resistencia que alcanzan hasta 2000 kg/cm² (200 MPa).
- Resistencia a tracción: proporcionalmente baja, es del orden de un décimo de la resistencia a compresión y, generalmente, poco significativa en el cálculo global.
- Tiempo de fraguado: dos horas, aproximadamente, variando en función de la temperatura y la humedad del ambiente exterior.
- Tiempo de endurecimiento: progresivo, dependiendo de la temperatura, humedad y otros parámetros.
- De 24 a 48 horas, adquiere la mitad de la resistencia máxima; en una semana 3/4 partes, y en 4 semanas prácticamente la resistencia total de cálculo.
- Dado que el hormigón se dilata y contrae en magnitudes semejantes al acero, pues tienen parecido coeficiente de dilatación térmico, resulta muy útil su uso simultáneo en obras de construcción; además, el hormigón protege al acero de la oxidación al recubrirlo.
FUNDAMENTOS DEL HORMIGON
FUNDAMENTOS DEL HORMIGON
El
hormigón en masa es un material moldeable y con buenas propiedades mecánicas y
de durabilidad, y aunque resiste tensiones y esfuerzos de compresión
apreciables tiene una resistencia a la tracción muy reducida. Para resistir
adecuadamente esfuerzos de torsión es necesario combinar el hormigón con un
esqueleto de acero. Este esqueleto tiene la misión resistir las tensiones de
tracción que aparecen en la estructura, mientras que el hormigón resistirá la
compresión (siendo más barato que el acero y ofreciendo propiedades de
durabilidad adecuadas).
Por
otro lado, el acero confiere a las piezas mayor ductilidad, permitiendo que las
mismas se deformen apreciablemente antes de la falla. Una estructura con más
acero presentará un modo de fallo más dúcil (y, por tanto, menos frágil), esa
es la razón por la que muchas instrucciones exigen una cantidad mínima de acero
en ciertas secciones críticas.
En
los elementos lineales alargados, como vigas y pilares las barras
longitudinales, llamadas armado principal o longitudinal. Estas barras de acero
se dimensionan de acuerdo a la magnitud del esfuerzo axial y los momentos
flectores, mientras que el esfuerzo cortante y el momento torsor condicionan
las características de la armadura transversal o secundaria.
Fisuras en el Hormigon
Las Fisuras en el Hormigón, son roturas que aparecen generalmente en la superficie del mismo, debido a la existencia de tensiones superiores a su capacidad de resistencia. Cuando la fisura atraviesa de lado a lado el espesor de una pieza, se convierte en grieta.
Las fisuras se originan en las variaciones de longitud de determinadas caras del hormigón con respecto a las otras, y derivan de tensiones que desarrolla el material mismo por retracciones térmicas o hidráulicas o entumecimientos que se manifiestan generalmente en las superficies libres.
La retracción térmica se produce por una disminución importante de la temperatura en piezas de hormigón cuyo empotramiento les impide los movimientos de contracción, lo que origina tensiones de tracción que el hormigón no está capacitado para absorber. En general, no conllevan riesgos estructurales y deben ser estudiados caso por caso, por ser atípicos.

Tratamiento de las Grietas
Por su naturaleza misma, ya que las grietas son debidas generalmente a fallas de diseño con insuficientes secciones de hormigón y/o armaduras de refuerzo, exigen trabajos importantes que incluyen re-calcular la estructura dañada y luego reforzar la misma.
enlaces:http://www.construmatica.com/construpedia/Fisuras_en_el_Hormig%C3%B3n
sábado, 6 de septiembre de 2014
Origen y evolución del hormigón armado
El hormigón o concreto se define como "un material compuesto empleado en construcción, formado esencialmente por un aglomerante al que se añade partículas o fragmentos de un agregado, agua y aditivos específicos". (wikipedia.com)
El aglomerante es en la mayoría de las ocasiones cemento (generalmente cemento Portland) mezclado con una proporción adecuada de agua para que se produzca una reacción. La mezcla de cemento con arena y agua se denomina mortero. Existen hormigones que se producen con otros conglomerantes que no son cemento, como el hormigón asfáltico que utiliza betún para realizar la mezcla.
La principal característica estructural del hormigón es que resiste esfuerzos de compresión, pero no tiene buen comportamiento frente a otros tipos de esfuerzos (tracción, flexión, cortante, etc.), por este motivo se debe usar de preferencia asociado a ciertas armaduras de acero, recibiendo en este caso el nombre de hormigón armado, o concreto pre-reforzado. Cuando se desea obtener una estructura de hormigón armado se establecen las dimensiones, el tipo de hormigón, los aditivos y el acero que hay que utilizar en función de los esfuerzos que deberá soportar y de las condiciones ambientales a los que estará expuesto.
http://es.wikipedia.org/wiki/Hormig%C3%B3n
A continuación agregaré un vídeo sobre el origen y la evolución del hormigón armado.
jueves, 4 de septiembre de 2014
Como se fabrica el Hormigon
https://www.youtube.com/watch?v=zNZAWKcpd98
miércoles, 3 de septiembre de 2014
TIPOLOGÍA DEL HORMIGÓN
Tipos de Hormigón
Hormigón ordinario: También se suele
referir a él denominándolo simplemente hormigón. Es el material obtenido al
mezclar cemento portland, agua y áridos de varios tamaños.
Hormigón en masa: Es el hormigón que
no contiene en su interior armaduras de acero. Este hormigón solo es apto para
resistir esfuerzos de compresión.
Hormigón armado: Es el hormigón que en
su interior tiene armaduras de acero, debidamente calculadas y situadas. Este
hormigón es apto para resistir esfuerzos de compresión y tracción. Los
esfuerzos de tracción los resisten las armaduras de acero. Es el hormigón más
habitual.
Hormigón pretensado: Es el hormigón que tiene en su
interior una armadura de acero especial sometida a tracción. Puede ser
pre-tensado si la armadura se ha tensado antes de colocar el hormigón fresco o
post-tensado si la armadura se tensa cuando el hormigón ha adquirido su resistencia.
Mortero: Es una mezcla de cemento, agua y arena
(árido fino), es decir, un hormigón normal sin árido grueso.
Hormigón ciclópeo: Es el hormigón que tiene embebidos en
su interior grandes piedras de dimensión no inferior a 30 cm.
Hormigón sin finos: Es aquel que sólo tiene árido grueso,
es decir, no tiene arena (árido menor de 5 mm).
Hormigón aireado o celular: Se obtiene incorporando a la mezcla
aire u otros gases derivados de reacciones químicas, resultando un hormigón
baja densidad.
Hormigón de alta densidad: Fabricados con áridos de densidades
superiores a los habituales (normalmente barita, magnesita, hematita.) El
hormigón pesado se utiliza para blindar estructuras y proteger frente a la
radiación.
martes, 2 de septiembre de 2014
Algo Más Sobre El Hormigón
HORMIGÓN
Mezcla de cemento, arena, grava o piedra triturada y agua. El cemento portland, que es el más importante componente del hormigón, puede adquirirse con facilidad, ya que existen numerosas fábricas que lo producen y lo distribuyen ampliamente. Por lo general, los otros componentes se hallan cerca del lugar de construcción.
El hormigón se prepara casi siempre en el mismo lugar de la obra. Después de mezclado, con una sustancia plástica a la que es posible darle con facilidad la forma que se desea. Sin embargo, después de fraguado adquiere una consistencia dura y resistente, por lo que soporta la acción del fuego y del agua, así como las inclemencias del tiempo y las presiones inertes y continuas.
Es por esto que se emplea mucho en la construcción de edificios, carreteras, pistas de aeropuertos, puentes, redes de alcantarillado y otras obras en las que los factores duración y resistencia son primordiales. Se usa también en la fabricación de partes prevaciadas, tales como bloques de construcción, y conductos para agua y desagüe. Se puede decir que el empleo del hormigón no tiene límites. Como quiera que se endurece al contacto con el agua, se utiliza en la construcción de muelles y espigones. Aun se emplea para hacer barcos durante contiendas bélicas prolongadas, cuando por lo general existe gran escasez de acero y mano de obra especializada. Los componentes del hormigón (cemento, arena, cascajo y agua) deben mezclarse en determinadas proporciones.
Durante la operación de mezcla, se produce una reacción química entre el cemento y el agua formando una pasta que al recubrir las partículas de arena y de cascajo hace que éstas se liguen entre sí y constituyan una masa sólida.
Para obtener una buena mezcla se deben seguir ciertas reglas. La más importante es no emplear mucha agua, puesto que la consistencia del hormigón se debe en gran parte a la fuerza adhesiva de la pasta formada por el cemento y el agua. Si se emplea esta última con exceso, la pasta de cemento resulta acuosa y débil. En cambio, si se ponen las cantidades adecuadas, la pasta liga bien el cascajo y la arena, resultando una masa fuerte y compacta.
El hormigón es muy resistente a la compresión, pero carece de elasticidad. En vista de que ciertas construcciones de hormigón (puentes, edificios, etc.) están sometidas tanto a esfuerzos de compresión como de tracción, se refuerza la masa de hormigón con barras o mallas de acero, para obtener un material de alta resistencia a la compresión y a la tracción. Este recibe el nombre de hormigón armado, y se emplea tanto en la construcción de partes simples como en obras de la magnitud de un rascacielos.
Suscribirse a:
Entradas (Atom)